non destructive hardness testing|types of hardness testing : private label Hardness testing can be considered non-destructive when used on the components’ surface and a hardness impression is not objectionable. Simple enough when the surface is typical of the bulk of the component and the configuration is accessible for performance of the test View and Download All American 50X Series operating instructions manual online. Electric Pressure Steam Sterilizers. 50X Series laboratory equipment pdf manual download. Also for: 50x-120, 75x series, 75x-240, 50x-240, 25x-240, .
{plog:ftitle_list}
Air removal verification testing should be performed daily to minimize risk of failure for prevacuum steam sterilizers. The presence of air in an autoclave sterilization cycle can adversely affect .The Bowie-Dick test is used to detect air leaks and inadequate air removal and consists of folded 100% cotton surgical towels that are clean and preconditioned. A commercially available Bowie-Dick-type test sheet should be placed in the center of the pack.
Nondestructive testing (NDT) or Nondestructive evaluation (NDE) is a method of materials testing to assess the characteristics of a component without altering or destroying it. NDT is important in the materials testing industry where quick, dependable information on .
What Is Rockwell Hardness Test? The Rockwell Hardness Test is one of several tests used to determine whether a material is solid and durable enough to be employed as a component of . Non-destructive Tests (NDT) Other testing methods, such as the X-ray and hydrostatic tests, are not destructive (NDT). . The hardness test usually applied is a nondestructive test, used primarily in the laboratory and not to any great extent in the field. Hardness tests are used as a means of controlling the properties of materials used for .
Non-destructive testing (NDT) is the analysis of the properties of a material, structure, or component without any physical damage to the system. . Hardness and Non-Destructive Testing (NDT) of Ceramic Matrix Composites (CMCs) Dragan Adamovic, Fatima Zivic, in Encyclopedia of Materials: Composites, 2021.Hardness testing can be considered non-destructive when used on the components’ surface and a hardness impression is not objectionable. Simple enough when the surface is typical of the bulk of the component and the configuration is accessible for performance of the test
The Vickers hardness test was developed in 1921 by Robert L. Smith and George E. Sandland at Vickers Ltd as an . 4 Apply the knowledge of Non-destructive testing in industrial sectors . Material Testing Lab 18MEL37A/47 A Dept. of Mechanical Engg, Atria Institute of . The Brinell hardness test was chosen to determine the hardness of the samples. Brinell testing is a destructive method widely used in industry to determine the hardness of metallic materials. The Brinell test is suitable for all steels with smooth surfaces of up to 650 Brinell hardness (HBW) .The Leeb hardness test is a non-destructive and portable method used primarily for metals. It involves a spring-loaded end with a spherical or conical indenter. The end that makes contact with the material is released, and the rebound velocity is measured after striking the material's surface. The Leeb hardness value is then determined based on .The specific size, shape, and location requirements of the hardness test determine the use of the Vickers method. One of the key advantages of the Vickers Hardness test is its versatility, as it can be applied to a wide range of materials and properties. Vickers Macro Hardness testing standards we work with: BS EN ISO 6507-1:2018 (HV1, HV5, HV10)
Non-Destructive Hardness Testing. Nondestructive testing (NDT) or Nondestructive evaluation (NDE) is a method of materials testing to assess the characteristics of a component without altering or destroying it. NDT is important in the materials testing industry where quick, dependable information on finished or raw material is needed. .
Destructive tests, such as tensile testing, impact testing, and hardness testing, are used to determine the mechanical properties, strength, durability, and other characteristics of materials. Destructive testing is often carried out during the design and development phases to ensure that the components meet specific performance requirements. NDT (Non-Destructive Testing) equipment refers to a wide range of tools and instruments used in various industries for inspecting and evaluating the integrity of materials and components without causing damage. These equipment are designed to detect defects, flaws, or irregularities that may compromise the performance or safety of the inspected objects.In the Brinell hardness test, a known load is applied for a given period of time to a specimen surface using a . Non-destructive testing methods require a trained and competent inspector. Moreover, the inspector must be trained in the specific testing method involved. Some of the most common non-destructive testing methods
Arguably, X-ray testing (or radiographic inspection) is the best, versatile, and widely used non-destructive test procedure. Mainly, it is used for figuring out the soundness of the welds. And no, we don’t mean externally — we mean internally. . Hardness Testing. In weld testing, the term hardness relates to the material’s ability to .
Material testing can be used to examine and evaluate a wide range of properties and characteristics of materials. With our measuring instruments, we test a material with regard to its resistance, strength, hardness, purity or resilience. As many methods there are for non-destructive material testing, as versatile are the areas of application . Request PDF | Hardness and Non-Destructive Testing (NDT) of Ceramic Matrix Composites (CMCs) | This article presents a short overview of the most common techniques in non-destructive testing (NDT .Non-destructive test (NDT) is a testing method that evaluates the physical properties of a material or component without causing any damage. In contrast, destructive tests (DT) involve assessing the properties and performance of materials and products by subjecting them to extreme conditions until they fail. . Hardness Testing. Hardness .Hardness Testing. Hardness testing is a non-destructive test method that involves applying a controlled constant load via a rounded or pointed object onto a metal surface, therefore creating an indentation. This indentation is then measured to determine the hardness of the material. This testing approach is used in a wide range of sectors for a variety of reasons and there are .
Non-destructive testing (NDT) stands as a crucial practice for ensuring the reliability and structural integrity of various materials and components without causing any harm. The evolution of NDT marks a significant advancement, empowering the evaluation and.NDT stands for Non-Destructive Testing. It is a wide range of techniques and methods used to evaluate the integrity, quality, and properties of materials, components, and structures without causing damage to the tested object. . Tensile testing, bend testing, impact testing, fracture toughness testing, fatigue testing, and hardness testing . Destructive testing involves causing damage to the material in order to test its limits, while non-destructive testing allows materials to be tested without causing any damage. Each type has its own advantages and disadvantages. Destructive testing is often more accurate than non-destructive testing but can only be used on a limited number of .
laboratory autoclave south africa
Non-Destructive Testing (NDT) is used in various industries to evaluate the properties of a material, component or system without damaging the test subject.NDT is also known by the terms Non-Destructive Examination (NDE), Non-Destructive Inspection (NDI), and Non-Destructive Evaluation (NDE).. In testing, troubleshooting, and research, NDT is a . Hardness testing can be applied to various types of materials, some of which are listed below: Metals and alloys. Ceramics. Elastomers. Polymers and plastics. Films. Rocks and minerals. Importance of Hardness Testing. Hardness testing is important for a number of different reasons. The hardness of a material can be a critical parameter in its .Common examples of destructive testing methods include tensile testing, hardness testing, impact testing, compression testing, fatigue testing, and chemical analysis. These tests provide valuable information about a material’s strength, ductility, hardness, fatigue resistance, fracture toughness, chemical composition, and other properties.During a hardness test we assess the depth of an indent or incision made by a precisely shaped indentor applied to the test material with a precise amount of. . Pro Integrity provides Non-Destructive Testing to Canadian companies that need to ensure the quality and performance of their industrial assets. Offering both regular inspection and .
Offering a full range of NDT services, we are experts in ultrasonic and radiographic testing. Still, our range of non-destructive testing capabilities extends further into dye penetrant testing, ferrite testing, hardness testing, visual testing/Replication NDT & more.. Amongst other services, we can offer you magnetic particle testing, liquid penetrant testing, acoustic emission test; We have . 1. Non-destructive Testing: Leeb Rebound Hardness Test, is one of the four commonly used methods to test the hardness of the metal. It is non-destructive used to inspect workpieces weighing above 1 kg. 2. Excellent portability: Unlike other traditional methods including Rockwell, Brinell and Vickers which were implemented only in the . Ultrasonic hardness testing is a non-destructive testing method that utilizes ultrasonic waves to assess the hardness of materials. Unlike traditional hardness testing techniques, such as indentation or scratch testing, ultrasonic hardness testing does not require physical contact with the material's surface. Instead, it relies on the .
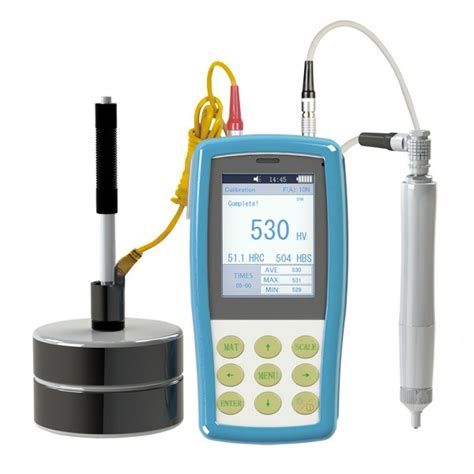
Such properties include hardness, resistance to penetration by projectiles, rebound capacity and ability to transmit ultrasonic pulses and X- and Y-rays. . Dynamic Non Destructive Test. At present the ultrasonic pulse velocity method is the only one of this type that shows potential for testing concrete strength in situ. It measures the time .
ultrasonic hardness testing
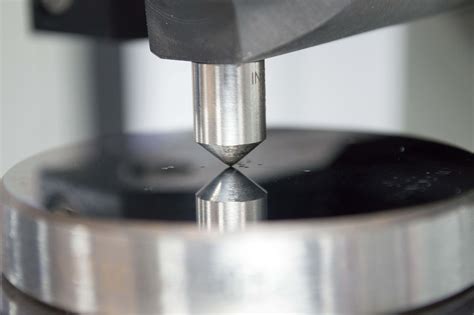
El documento presenta la ficha técnica del agua desionizada, un producto purificado por destilación, osmosis inversa o intercambio iónico con bajo contenido microbiológico y ausencia de patógenos. Se recomienda su uso .In this article, we will discuss the topic of what type of water should be used in the autoclave, providing the different types of water used in autoclaves and their importance in .
non destructive hardness testing|types of hardness testing